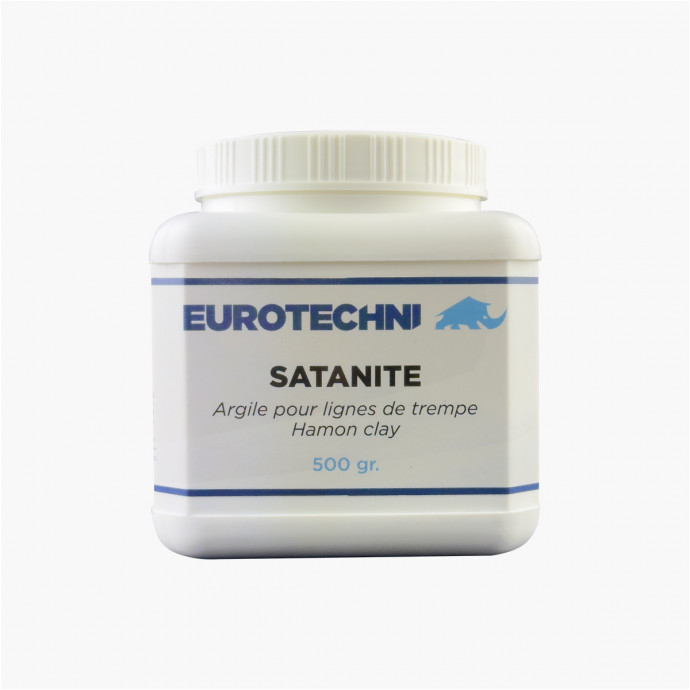
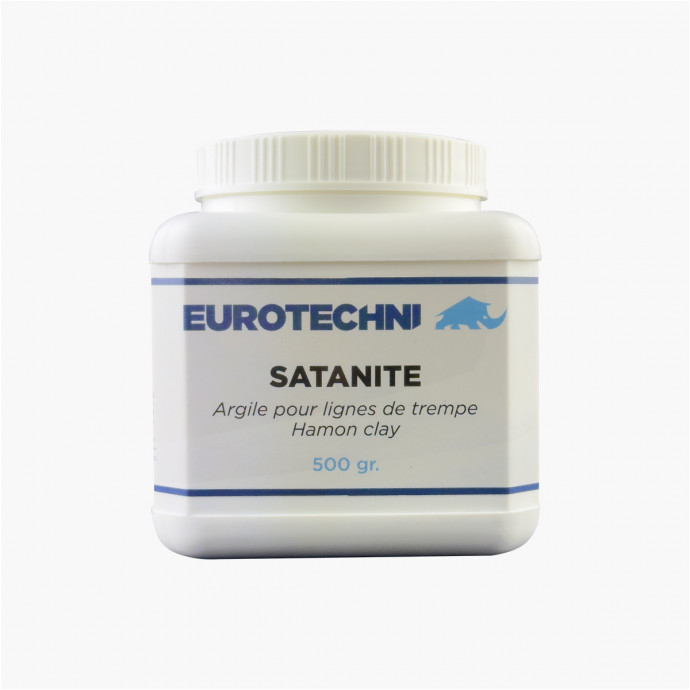
EUROTECHNI IS PROUD TO PRESENT YOU ITS BRAND NEW WEBSITE!
Selective quenching lines, or "hamons" (.
The differentiation of heat treatment according to areas defined by the craftsman reveals more or less brilliant lines and contrasting tints of steel.
They are arranged along the length of the blade, along the edge.
In the soaking process, the non-insulated part of the blade will be cooled quickly while the isolated part will take longer.
Beyond an undeniable aesthetic quality, the realization of genuine hamons, or selective dip lines, allows to obtain an extremely hard edge while maintaining all its flexibility to the rest of the blade. Technically, the risks of blade rupture are greatly reduced.
Not all steel grades are suitable for selective quenching. The carbon steel shades of simple, very low alloy composition should be given priority.
Thus, XC100 carbon steels and C130 will yield excellent results, because they are heavily charged with carbon. The XC75, although less carbon-based, may also be interesting.
The dip lines, or "hamons", are obtained by applying a more or less thick layer of refractory mortar to the blade, which will serve as thermal insulation at the time of soaking.
Applied with an artist-painting brush or knife, the refractory mortar is spread into a layer covering the part of the blade to be insulated thermally, so as to constitute a protective gangue.
Made from natural or synthetic clays, the refractory mortar is obtained by mixing with other ingredients such as charcoal and silica.
Depending on the mortar composition, the thickness required for a good thermal protection efficiency can be up to 3 cm.
The Satanite proposed by Eurotechni consists of an optimized mixture in the form of Kaolin powder (refractory white natural clay), Mullite (refractory synthetic clay used in the manufacture of melting crucibles) and silicas (Quartz, Cristobalite). Easy to implement and economical, Satanite requires a maximum thickness of only 1 mm for efficient thermal protection.
To achieve the best possible results, a few steps must be taken to correctly use Satanite. Below are some tips from Tanguy Coillot, Lorrain cutlery whose work you can enjoy on its website, Facebook page and Instagram page.
First, dilute Satanite in water, in an airtight container, until you get a creamy, almost liquid consistency.
The blade on which you wish to apply Satanite must be properly degreased, and move with a large grain (60) so that it hangs properly.
Apply the Satanite in a thin layer (1 mm maximum) on the first face of your blade and dry it. You can speed up the drying of Satanite by using a heat stripper – let cool well after the operation.
Repeat the operation on the second side of your blade.
Do not forget to apply Satanite also on the back of the blade, so that the layers do not take off during heating and soaking.
When the Satanite is dry, you can do the soaking: bake your blade during the recommended holding time, then dip it into the soak oil – preferably use accelerated soak oil, such as INO 235 quench oil. The latter must be heated to about 40°C before immersion.
Once the blade comes out of the oil, you can remove Satanite by scratching and pass your blade backstand, to control the appearance of your hamons. If the result satisfies you, then go to the income of your blade.
You can store diluted Satanite in a watertight container for future use. If you see that it has dried, you can completely add water and mix it so it can be used again.
After the complete thermal treatment of the blade (trempe and reed), the definitive revelation of the dip lines, or hamns, marks the last step before its final polishing and sharpening.
Different methods are possible.
However, we recommend following the following operations to achieve good results:
• Use liquid or powdered iron perchloride.
• Several iron perchloride baths will be necessary for your blade to achieve an optimal result. We recommend 10 iron perchloride baths of 45 seconds each. The number of baths can be reduced by an increase in the duration of immersion of the blade.
• Between each iron perchloride bath, rinse and clean the steel wool blade 000 or 0000.
• When the successive baths are completed, neutralize the acidity of the iron perchloride on the blade with soapy water or dishwashing liquid and dry.
We have reached the end of the process of making dip lines or hamons and all that remains is to mount the blade of the knife and... admire a result as unique as it is spectacular.
© Copyright 3801 - Total or partial reproduction prohibited without authorisation by EUROTECHNI S.A.S